The Three Main Types of Facility Layouts
Apr 5, 2024
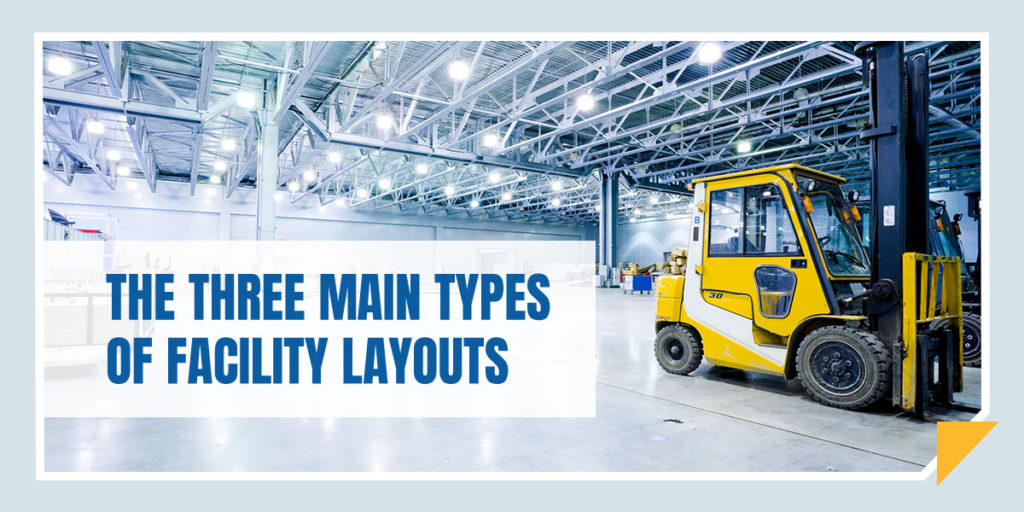
Facility layouts refer to how workers, machines, equipment, and products are organized in a facility. The most effective layouts enable efficient workflows without disruptions to improve a facility’s operational flexibility and reduce downtime. The best layout depends on the workflow and the company’s nature of operations.
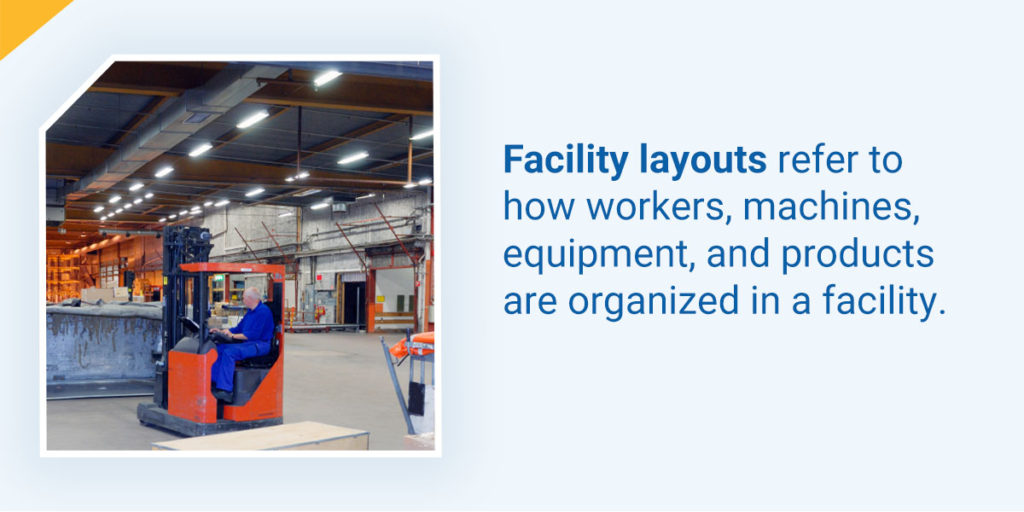
Facility layout planning or strategizing involves physically arranging all production factors to ensure operations are aligned with the organization’s objectives. It also takes into consideration the available space and the nature of the products you work with. The objective of the layout strategy is to optimize space utilization, improve productivity and enhance material handling.
3 Main Types of Plant Layouts
There are three main types of facility layouts suitable for different types of production facilities. These plant layouts maximize productivity, workflow, and available space, and each has its own advantages and disadvantages. The three main types of facility layouts are:
1. Process Layout
The process facility layout, also known as functional layout, involves arranging employees, tasks, and machines according to the nature or type of operations. The process layout is best for a company that has low-production volume facilities and non-repetitive tasks. The workflow revolves around the production process and follows a logical sequence of production activities. For example, in welding facilities, grinding is completed in one area, assembling in another, and inspection in a different location.
It’s an incredibly flexible layout that allows placing different machines at various locations. The machines produce different products, and the products move from one workstation to another without stopping at every station. They utilize general-purpose machines that easily adapt to new operations and product designs. Every worker in the process layout facility has a unique role in the production process.
Advantages of process layout include:
- Ideal for small production volumes
- Suitable for non-repetitive activities
- Ensures efficient utilization of equipment
- Reduces initial equipment purchase costs
- Decreases duplication of machines
- Reduces downtime because work can be transferred to other machines when one fails
- Boasts greater flexibility in manual labor and equipment
Disadvantages of process layout include:
- Requires extensive floor space
- Because work does not flow through definite lines, scheduling can be difficult
- It’s ineffective and inefficient for the production of standardized products
- Longer total production cycle time
2. Product Layout
The product layout design arranges activities, machines, and materials on a production line according to the sequence of operations necessary to assemble a product. In this layout, products move in one direction and pattern on the assembly line. You might see this referred to as the line layout. The idea of this facility layout is to utilize the output of one machine as a raw material in the next machine.
It’s an autonomous layout most suitable for repetitive operations and mass production facilities. It’s only efficient in operation plants that produce standardized products. The product layout is often used in service companies for routine processing operations. It’s also suitable for food processing plants and appliance and automotive manufacturing facilities.
Advantages of product layout include:
- Requires minimal manual work
- Reduces the scope of human errors on the production lines
- Allows better utilization of human resources and machine power
- Enhanced automation minimizes total production time
- Enables smooth and continuous workflows
Disadvantages of product layout include:
- Increased downtime resulting from power fluctuations and machine breakdowns
- Requires highly-trained workers to operate the machines
- Requires high initial investment and a large space for all the equipment
- The manufacturing costs increase with lower production volumes
- It’s inflexible and may easily result in bottlenecking and production downtime
3. Fixed-Position Layout
With the fixed position layout, the product stays in one place while the workers, material, and equipment move to it as necessary. The product remains stationary either because it’s too big, heavy, or fragile to be moved around during assembly. Sometimes the fixed position layout is utilized when there’s limited space on a site, so parts are produced on other sites and brought to the main site for assembly. The fixed-position layout is often utilized when producing ships, aircraft, automotive, and construction projects.
Advantages of fixed position layout include:
- Reduced fixed costs, such as material handling expenses
- Allows more customization opportunities
- Reduces the risks of product damage during shipping or transportation
- The independent production lines can reduce the total cost of production
- It allows greater flexibility in terms of production volume and product design
- Enables effective scheduling and planning
Disadvantages of fixed position layout include:
- Demands highly skilled manual work
- Reduced productivity and efficiency because of time spent moving product parts to production centers
- High variable costs, such as the costs of moving equipment around a facility
- Time-consuming because of the movement of machine equipment
A Mobile Solution: Gantry Cranes
In all three types of facility layouts, flexibility is a major concern. Flexibility is crucial to minimize the distance that materials need to move around a facility and ensure optimal space utilization. Gantry cranes can be used to increase flexibility in manufacturing facilities using any of the three layouts. These are overhead cranes with legs to support their hoist, bridge, and trolley, meaning they can move around a facility to lift and move heavy materials.
Gantry cranes make any layout adaptable because they don’t need to be attached to a building’s support structures. They can also be assembled and disassembled easily to be used in different work areas. For example, you can use gantry cranes with a fixed-position layout where parts are produced and assembled at different sites. Instead of having different gantry cranes in various locations, you can move with your crane from site to site.
Gantry cranes can also be used in the process layout design to enhance flexibility in material handling without rearranging the operations. Spanco has a series of gantry cranes that can be used to move the material to the product to ensure continuous workflows and reduce downtime. Our cranes don’t travel along a fixed path and allow clear passages underneath a wide variety of loads.
Achieve Unmatched Flexibility With Spanco Gantry Cranes
Instead of changing your entire facility layout to improve flexibility, invest in gantry cranes. Gantry cranes introduce a new layer of flexibility without rearranging the flow operation in your facility and at a fraction of the cost. Spanco is a reliable manufacturer of material handling machines such as gantry cranes to move and secure materials and machines in facilities.
Our gantry cranes are suitable for use in a wide range of industries and compatible with all facility layouts. They adhere to American National Standards Institute (ANSI) standards and the Occupational Safety and Health Administration (OSHA), so you can rest assured your workers stay safe. Contact us online today or select your preferred gantry crane system using our system selector tool.
Categories
Share this post
Contact us
Looking for the perfect fall protection equipment? Let us help!