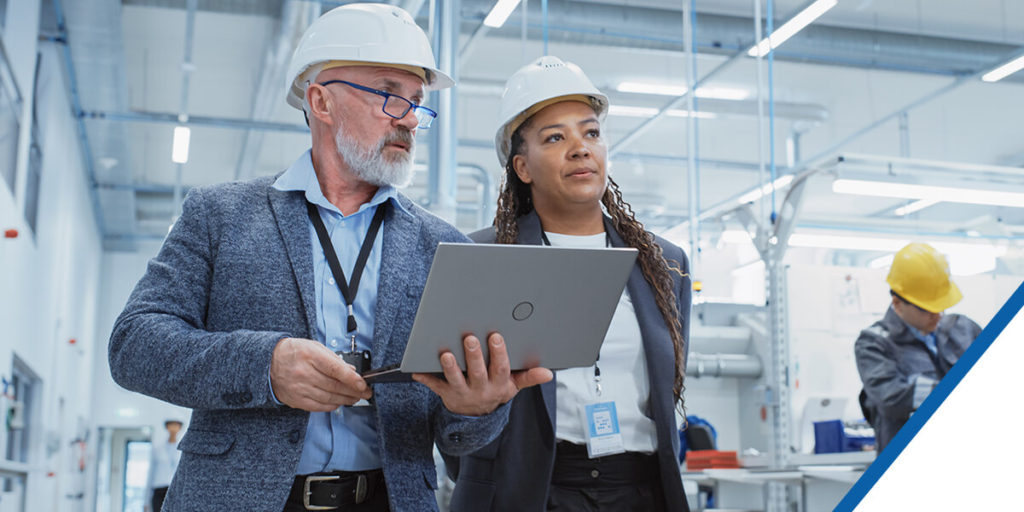
Manufacturing Facility Layout Plan
Jun 4, 2024
A manufacturing facility’s layout determines many aspects of production. By optimizing the arrangement of equipment, workers, and materials, you can make the most of your available space. An effective facility layout can help improve productivity, reduce downtime, ensure employee safety, and streamline workflows and operations.
Since the layout of manufacturing facilities can vary widely, creating a plan requires careful evaluation of your existing space, business goals, and options.
Factory Layout Objectives
A production facility layout must consider a set of objectives addressing productivity, efficiency, and effectiveness. Effective manufacturing operations should utilize space efficiently and minimize material handling costs by:
- Ensuring efficient labor use and reducing repetitive and nonproductive tasks.
- Preventing downtime and bottlenecks to support high-quality, streamlined production.
- Ensuring clear and concise communication between workers and supervisors.
- Facilitating continuous material and product movement.
- Considering flexibility for future workflow changes.
There are several ways to ensure your facility meets the above requirements to design an effective layout. These methods include:
- Providing more thorough employee and supervisor training.
- Building awareness of safety hazards and protocols.
- Implementing automation technology to maximize efficiency, reduce downtime, and save money.
- Organizing stations and equipment to facilitate workflow.
Design Factors to Consider
Before you start designing your manufacturing facility layout plan with these goals in mind, consider a few key factors to make the best use of your space. The variables to consider when creating a new production facility layout include:
- Use of space: Unless you plan to expand your facility soon, you’ll have to get creative with what you have. Your factory layout should strategically use every square inch of available space.
- Efficiency: It’s important to design your floor plan to make everyday tasks as efficient as possible for crew members. For instance, you might place an automation system strategically to reduce the difference between two processes and increase productivity. Additionally, forklifts should be easily accessible to transport materials and dispose of waste as needed.
- Accessibility: There should be sufficient space between elements to ensure an accessible floor plan for all employees. Material handlers require plenty of room for themselves and the items they’re transporting around the facility.
- Flexibility: Your plant layout should allow ample flexibility for future growth and expansion. Make sure the floor plan won’t constrict your operation. This doesn’t mean you must accurately predict how much you’ll grow within the next few years. Just keep future growth opportunities in mind when designing the layout, considering a rough estimate. For instance, you might factor in the potential for 30% facility growth when mapping your new design.
- Operator-first mindset: Every facility is unique in its operations and won’t benefit from a cookie-cutter approach, so it’s essential to design a plant layout with your applications in mind. Consider your operators’ daily tasks and what changes would support their jobs. Designate areas for different manufacturing processes and finished products. Will completed products move to the next cell or into dispatch? An effective facility layout speaks to your team’s and company’s needs.
Four Basic Types of Layouts
Depending on their operations, a facility manager should choose a layout that provides the highest efficiency while reducing time, labor, and costs. There are four basic production facility layouts used in manufacturing, all with the objective of meeting the above requirements.
1. Product Layout Design
Product layout design is a popular manufacturing facility layout. Also called assembly lines, product layouts arrange activities in a production line according to a sequence of operations needed to assemble a particular product. It’s an effective facility layout for mass production or repetitive operations with steady demand and high volume. Therefore, it’s more autonomous than other designs.
A product layout design moves materials in one direction and pattern along the assembly line. The main concern in this layout design is balancing the assembly line so workstations don’t hold up workflow through the line. While it provides efficiency and ease of use, its main disadvantage is inflexibility.
There are ways to improve layout functionality and flexibility for manufacturing facilities using a product layout design. Some facilities use conveyor belts to ensure continuous material and product movement along a fixed production path. However, the problem with using conveyors in some applications is that processes can’t be changed or altered for future workflow. Furthermore, aisles can be narrow, and floor obstacles may interfere with material flow on the ground, potentially creating bottlenecks.
Incorporating an overhead monorail system is a good way to increase manufacturing flexibility. Today’s monorail systems are not only designed to move products down a fixed production path — they are also designed for increased flexibility and future workflow change.
Monorails can be ceiling-mounted or freestanding, depending on the facility’s needs. A freestanding system is ideal if you’re dealing with multiple overhead obstructions. However, most product layout manufacturing facilities have floor obstructions and narrow aisles. In this case, a ceiling-mounted monorail is the most versatile and ergonomic way to streamline production and improve flexibility.
2. Process Layout Design
A process or functional layout is ideal for non-repetitive tasks in low-production-volume areas due to its flexibility. As the name suggests, a process layout centers workflow around the manufacturing process and groups employees performing similar tasks. Products flow from one workstation to another but may not go to every station. You might have one station for inspection, one for assembly, and so on.
Process layouts are suitable for factories producing small numbers of various products. They often incorporate general-purpose machines that easily adjust to new product designs and operations. For instance, a custom machinery manufacturer would benefit from a process layout.
3. Fixed-Position Layout Design
In a fixed-position layout, the main production process element remains in a fixed position. Workers must bring other materials, parts, tools, equipment, and machinery to the site. Assembly line movement around a plant doesn’t work for some products, such as planes and ships.
A fixed-position layout allows these items to stay in one location while machinery and employees move to them as needed. Limited project site space typically means some product parts must be assembled at other sites and then moved to the fixed-position site for assembling. This layout is also a common solution for on-site services like construction projects, landscaping, housecleaning, and pest control.
4. Combination Facility Layout
A combination or cellular facility layout integrates two or more of the above designs based on the factory’s requirements. Many cellular layouts combine aspects of fixed-position and product layouts. They feature compact, self-contained work cells with several employees and machines arranged sequentially.
Each cell performs most or all of the tasks needed to fulfill a manufacturing order. The idea is to build a team-oriented environment where every member is involved in production from start to finish. To achieve maximum work efficiency, companies with cellular layouts train employees to perform multiple tasks, and each team monitors its own product quantity and quality.
A combination layout offers several advantages, like reduced inventory levels and completion times, excellent quality, and high employee morale. Whether a large aerospace manufacturing company or a small factory that produces robot components, many factories can benefit from adopting a cellular layout.
Steps for Designing a Manufacturing Facility Plan
Designing the most efficient and effective manufacturing facility layout can be a meticulous process. It typically includes the following steps:
- Collect background information. Review your objectives, needs, and facility layout basics, such as how much space you have, the desired workflow, and the equipment you will use. These considerations help ensure your manufacturing facility layout aligns with your production goals.
- Make a plan. Create a process flow chart that details the key processes, equipment, decision points, and material handling requirements. You should also document how the materials will move through the different production lines to ensure the most efficient use of facility space and resources and minimize waste.
- Build a rough layout. Create 2D and 3D layout templates that provide an idea of how the layout will turn out, how the equipment moves, and how work flows through the production line. These templates also help to ensure dimensional accuracy in the final facility layout.
- Choose your equipment. As you select your equipment, consider the size of the space, equipment dimensions, and desired workflows. Go with equipment you can easily arrange in a logical and lean-focused way to improve worker productivity and enhance their safety as they move between machines and workstations. Also, think of how each piece of equipment blends into the workflows at your facility to maximize efficiency and profitability.
- Refine your layout. Choose an effective manufacturing layout design by considering the products, processes, and process flows involved in your production line. The right layout design optimizes flow in the facility and may involve changing equipment, storage, and walkway locations. The best layout type for your organization should also consider the nature of your operations, product variety, and production volume.
- Review workflows. Select a layout shape that aligns with the flow of materials and processes at your facility. Some of the main layout shapes include U-shaped, S-shaped, straight line, convoluted, and 3D layouts.
- Simulate activities. Set up a 3D simulation video to test how the equipment, raw materials, and products move down the production line. It also helps you identify bottlenecks and eliminate them before they start impacting and slowing down the production line. The simulation also helps you identify opportunities to improve the layout and adopt a lean manufacturing system.
- Consider future needs. Be sure to leave ample space to accommodate future expansions and renovations without extended downtime. This means adopting a flexible layout with several pathways for material flow that allows you to respond quickly to industry or company-specific changes.
- Confirm your alignment. Verify that the final layout meets the manufacturing facility’s objectives, including efficiency, flexibility, and safety.
Build an Effective Facility Layout With Spanco, Inc.
As technology constantly grows and changes, manufacturers should consistently improve their operations and streamline production. Rather than redesigning an entire manufacturing facility, incorporating a flexible material handling solution is an economical way to redefine your workflow and introduce a new layer of flexibility. Material handling equipment also improves staff efficiency and productivity.
At Spanco, we have a variety of material-handling products to help optimize plant efficiency. Whether you need an overhead Gantry Crane to transport heavy materials or a Jib Crane for more articulated handling, we can help you find the equipment you need to move manufacturing materials with ease. Our team of experts will help you select the best material handling equipment and install and maintain these to reduce downtime and ensure peak productivity.
Browse our product inventory or contact us to find the right solution for your needs.
Categories
Share this post
Contact us
Looking for the perfect fall protection equipment? Let us help!